April 2019 Articles:
- UNDERSTANDING NATURAL GAS FUEL RELIABILITY FOR BACKUP POWER
- COMPLYING WITH NEW FLORIDA BACKUP POWER RULES
- DEMAND RESPONSE 101
- PRIME POWER, CONTINUOUS DUTY & CHP SOLUTIONS WITH SIEMENS
UNDERSTANDING NATURAL GAS FUEL RELIABILITY FOR BACKUP POWER
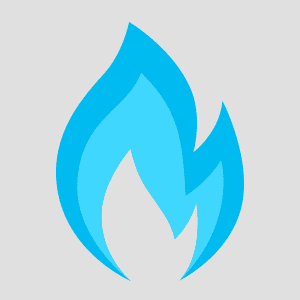
Reliability of fuel supply tends to be of great concern for authorities having jurisdiction (AHJs). Typically, AHJs require the use of on-site fuel for facilities that are categorized as NFPA 110, Level 1 loads; these are defined as backup power systems installed “where failure of the equipment to perform could result in loss of human life or serious injuries.” NFPA 110 Level 1 loads are typically associated with NFPA 70: National Electrical Code (NEC), Article 700: Emergency Systems. Mission-critical applications like these, which include hospitals and 911 call centers, rely on diesel-fueled generators because on-site fuel storage is perceived to be more reliable.While NEC requires an on-site fuel supply for mission-critical and legally required standby systems, it allows the AHJ to permit the use of other than on-site fuels in applications that have a low probability of a simultaneous failure of both the off-site fuel delivery system and the power from the outside electrical utility company. However, storing diesel fuel on-site is seen as increasing the reliability of backup power in non-code-required applications, and makes it possible to provide backup power in remote areas that do not have access to a gaseous-fuel infrastructure.Traditions are typically hard to break, which could explain why many AHJs continue to require diesel-fueled gensets. Diesel has been the traditional fuel of choice for backup and standby gensets. Historically, the use of diesel as a fuel for gensets has been a long-standing, proven technology. Because of this, the perception within the market is that diesel engines are the most reliable prime movers for backup power applications.DIESEL FUEL CONCERNS
While many users may prefer diesel as a genset fuel, several issues associated with diesel should be considered. Annex A of NFPA 110 identifies several considerations associated with diesel fuel. For example, temperature variations can accelerate fuel degradation. Prolonged exposure to ambient air can cause diesel fuel to oxidize. Ambient temperature changes can lead to condensation within the fuel tanks. The water from this condensation can lead to microbiological contamination and growth, which in turn can cause corrosion of steel tanks and components, filter plugging, operational issues, or a hydrocarbon release to the environment.For these reasons, facility managers must be diligent in maintaining their generators’ diesel fuel supply. Even in ideal cases, diesel fuel has a shelf life of less than 12 months, at which time the fuel must be polished (filtration and water removal) or replaced. Ultra-low-sulfur fuel is particularly prone to fuel breakdown, because the extra refining steps required to remove sulfur also remove some of the elements that keep the fuel stable.
Despite their widespread use, diesel fueled gensets are vulnerable to events that could cripple transportation infrastructures, making refueling problematic—or perhaps even impossible. Hurricanes and severe storms can close roads. Grid failures can make it impossible for suppliers to pump fuel into delivery trucks. For example, Hurricane Sandy, which slammed into the Northeastern U.S. in late October of 2012, caused significant damage to fuel distribution infrastructure. Fuel distribution networks were paralyzed. Critical terminals for petroleum and petroleum products were badly damaged. Many service stations lost power and couldn’t pump gas or diesel fuel. Whereas diesel gensets can operate reliably during extended outages, users can’t always count on the availability of diesel fuel and deliveries.
RELIABILITY OF THE NATURAL GAS INFRASTRUCTURE
While weather, human-caused disasters, and even labor issues such as strikes can impact diesel fuel delivery and availability, the natural gas utility infrastructure is generally reliable. Typically, factors that tend to impact the electrical infrastructure do not impact the natural gas infrastructure. In most cases, natural gas is delivered by underground pipelines that are usually not affected by severe weather that can cause electrical power outages.
According to Platts, the natural gas supply throughout the Northeast U.S. was not interrupted during Hurricane Irene, which hit the U.S. in late August, 2011. A check of natural gas pipelines throughout the Northeast area showed no notices of service interruptions or other issues.
An analysis of the Northeast snowstorm that occurred in late October, 2011 by the Federal Energy Regulatory Commission (FERC) and the North American Electric Reliability Corporation (NERC) showed that more than 3 million customers lost electric power. However, the analysis made no mention of any natural gas infrastructure interruptions. After Hurricane Sandy, New Jersey Natural Gas reported that it was shutting off service to about 28,000 customers because of storm damage. However, the number affected by this outage was only a fraction of the nearly 2 million New Jersey customers without electrical power. Using natural-gas-fueled gensets instead of diesel-fueled gensets depends on the intended application. What this means is that, unless the AHJ allows otherwise, mission-critical applications require on-site fuel storage, or diesel. However, for non-coderequired applications, natural gas can be a viable option. Storage is not an issue because natural gas is supplied continuously by the local municipal infrastructure. This means that this continuous supply extends genset run time.
REGULATORY ISSUES
Numerous NFPA codes and standards apply to standby generators. NFPA 110 and the NEC are the most frequently referenced standards for ensuring safe, reliable, and compliant genset specification, installation, commissioning, and operation. Most of the requirements applicable to genset fuel refer to diesel-powered units. However, there are provisions and exceptions associated with natural gas-powered units.
According to NFPA 110, Article 5.1.1(3), natural gas is an acceptable fuel for an emergency power system. However, the exception that immediately follows states: “For Level 1 installations in locations where the probability of interruption of off-site fuel supplies is high, on-site storage of an alternate energy source sufficient to allow full output of the EPSS to be delivered for the class specified shall be required.”
While most of NFPA 110 applies to diesel fuel delivery, storage, and quality requirements, Article 7.9 includes specific requirements for natural gas:
7.9.7—Where the gas supply is connected to the building gas supply system, it shall be connected on the supply side of the main gas shutoff valve and marked as supplying an emergency generator.
7.9.8—The building’s main gas shutoff valve shall be marked or tagged to indicate the existence of the separate EPS shutoff valve.
7.9.9—The fuel supply for gas-fueled and liquid-fueled prime movers shall be designed to meet the demands of the prime mover for all of the following factors:
1) Sizing of fuel lines
2) Valves, including manual shutoff
3) Battery-powered fuel solenoids
4) Gas regulators
5) Regulator vent piping
6) Flexible fuel line section
7) Fuel line filters
8) Fuel vaporizers (LP-Gas)
9) Ambient temperature effect of fuel tank vaporization rates of LP-Gas where
applicable.
While NFPA 110 has plenty to say about genset fuel systems, the NEC has very little. NEC, Article 700.12(B)(3) states: “Prime movers shall not be solely dependent on a public utility gas system for their fuel supply.” However, the exception that immediately follows states: “Where acceptable to the authority having jurisdiction, the use of other than on-site fuels shall be permitted where there is a low probability of a simultaneous failure of both the off-site fuel delivery system and power from the outside electrical utility
company.”
ADDRESSING NATURAL GAS RELIABILITY WITH THE AHJ
The AHJ has the final say regarding genset applications. Therefore, consulting the AHJ regarding the reliability of the genset’s fuel supply is a must.
Because of its availability, many AHJs prefer on-site fuel storage, meaning diesel fuel. It is generally required by the NEC, Article 700 in many municipalities. However, convincing the AHJ to consider approving the use of natural gas-fueled gensets may be quite challenging. While most AHJs do not have to be convinced that diesel fuel is reliable, providing proof that the natural gas fuel source is reliable may open eyes and change minds.
One way to convince the AHJ to consider natural gas is to get the utility to certify reliability. The reliability of a natural gas fuel source can be proven with a letter from the natural gas vendor that contains:
• A statement that the fuel source is reasonably reliable
• A description supporting the assertion that the source is reasonably reliable
• A statement of the low likelihood of an interruption
• A description supporting the assertion that the likelihood of interruption is low
• A signature from technical personnel
Working with both the local gas utility and the AHJ can help engineers, owners, and operators understand the reliability of the natural gas supply as it compares to on-site diesel fuel. Ensuring that the facility is not subject to curtailment policies can help prevent natural gas fuel supply interruptions.
Another way to alleviate discussions about the reliability of on-site vs. utility-supplied natural gas is to consider a system that uses both fuels—individually or simultaneously. Bi-fuel gensets, for example, run on both diesel fuel and natural gas and leverage the benefits of each while minimizing their respective drawbacks.
Bi-fuel gensets combine the power density and capital cost benefits of diesel engines with the extended run time of natural gas. These units start up on diesel fuel, which helps gensets meet the 10-second startup requirements for mission-critical facilities. As loads are added, natural gas is introduced and increased while diesel fuel is decreased. Typically, bi-fuel gensets operate on up to 75% natural gas, 25% diesel with no reduction in power under typical load conditions. However, bi-fuel units will not run on 100% natural gas.
Because less diesel fuel is consumed, run times are significantly extended, which could be a significant issue during emergencies that challenge municipal infrastructures, thereby affecting diesel fuel deliveries. With natural gas as the predominant fuel, diesel tanks can be smaller, which reduces the risk of fuel contamination as well as the cost of maintaining diesel fuel.
Bi-fuel gensets are only slightly more expensive than diesel-only units. Also, fuel redundancy is built in. In the unlikely event that the natural gas supply is interrupted, or if there is a fault in the bi-fuel delivery system, the genset controls automatically revert to all-diesel operation without interruption.
CONCLUSION
For decades, diesel has been the traditional fuel of choice for commercial and industrial backup and standby gensets. However, today, diesel is not the only option. Now, engineers, owners, and operators have genset fuel choices, each of which offers unique benefits.
Take time to learn how these genset fuel choices can be applied to ensure that the best solutions are selected. Also, consult the local AHJ to understand the policies on using particular fuels in given applications.
COMPLYING WITH NEW FLORIDA BACKUP POWER RULES
John Sharpe: Power Solutions Manager – Generac Power Systems
Hurricane Irma left a trail of destruction in its path. Irma was the strongest Atlantic storm in over a decade and made landfall in Florida on September 10, 2017. The port of Miami was closed for three days. About 7.7 million customers lost electricity in that time. Two days after landfall, 4.4 million people were still without power. The estimated damage from the storm was $53 billion to the state of Florida and 84 fatalities were tied to the storm statewide.
The health care industry took a major hit from the storm as well. In total, 350 of the 700 nursing homes lost power and 88 facilities had to be evacuated. Of the 3,100 assisted living facilities, 1,677 lost power and 635 had to be evacuated. The Rehabilitation Center at Hollywood Hills suffered the biggest loss when they were without power for more than three days. The 152-bed privately owned nursing home had no air conditioning because it was not connected to an emergency generator. As a result, 12 residents died of heat related issues attributed to the hurricane.
Six days after Irma made landfall, on September 16, 2017, Governor Rick Scott issued an emergency order for generators, requiring every nursing home and assisted living facility in the state to have the equipment. The measure was ratified by the state legislature in March of 2018. Facilities were required to file an Emergency Power Plan (EPP), they had to identify a cooling space for all patients/residents, and they are required to maintain 81°F for 96 hours in the event of a loss of normal power. The target enforcement date for the law was June 1, 2018 and the necessary equipment needed to be installed and operational by January 1, 2019.
Before Irma, Lourdes McKeen Towers already had a system in place. They had two incoming utility services from serving utility pad mounted transformers. They had a 600 kW diesel generator for essential electrical systems and life safety. A 4,000-gallon underground diesel fuel storage tank was also included. Prior to the storm, the facility investigated improving their generator system. The governor’s new law moved the system from “wish list” to mandated. After review and discussion of the direction, they wanted to take the new system, the lifeboat and cooling-only solutions were not desirable to the facility management, instead they wanted a whole-house solution.
“An existing generator had been on the property for 20 years,” said Pace Alford, executive director, Lourdes McKeen Towers. “It was a standard diesel generator that powered up only key emergency systems. The generator would only run limited key systems like strategic red plugs, elevators, dining, limited lighting and life safety systems. A key problem was the system didn’t run AC systems, which is now required by state law.”
The new system design was complicated and came with some technical challenges. The design team had to find space for the generation system and distribution equipment. They determined there would be an impact on the existing underground parking garage by taking several spaces meant for residents and employees to help support the generator. The team then had to determine how much more fuel would be needed in conjunction to the existing 4,000 gallon storage tank. They also had to determine a plan for performing the installation while keeping the facility in operation 24/7, which required a temporary utility tie-in or a mobile generator.
Many factors pushed for Lourdes McKeen Towers to pursue a turnkey solution. “We wanted to turn the generator system into not just a part of the plant operation makeup of the facility, but a marketable piece of the community,” said Alford. “As these power regulations develop people want to know that communities will not just keep the air on or meet the bare minimum standard required by the state, but will go above and beyond for the care of their loved ones.”
When analyzing the best solution for this project, utility data showed an annual maximum peak of 1124 kW was used. The design team looked at two possible solutions based on that knowledge. The first was a single 1500 kW generator. It would be 520” in length across five parking spaces. With no fuel, the unit would weigh 52,000 lbs., with fuel it would weigh 73,000 lbs. The other option was a Modular Power Solution (MPS) consisting of three 500 kW generators. The solution would be 408” in length spanning three parking spaces. The units would weigh 45,000 lbs. with no fuel and 66,000 lbs. with fuel.
In the end, McKeen Towers went with the MPS bi-fuel solution. “Pre-Irma goal was a new generator plant for the entire building,” said Alford. “To meet that need we would have to have substantial fuel storage and the governor’s order guidelines made it difficult for us to meet that goal. The bi-fuel system helps not only meet, but exceed the governor’s mandate by providing additional protection through fuel redundancy.” Despite the perceived value of having diesel fuel on-site for reliability, power outages can damage infrastructure and make diesel refueling difficult or impossible. Generac bi-fuel generators mitigate refueling issues by operating primarily on utility-supplied natural gas. A bi-fuel generator starts on diesel fuel and adds natural gas as load is applied, until the unit runs primarily on natural gas. Bi-fuel generators do meet the on-site fuel requirements for emergency systems as referenced in NEC 700 and NFPA 110. With less diesel fuel required to be stored on-site, permitting also becomes easier. The onsite fuel requirement for this project called for 6,826 gallons. In addition to the 4,000 gallon UST, three 1,000 gallon day tanks were added, providing 161 hours of run time.
“The project has been received overwhelming positive by our residents, guests, prospective residents, and the state of Florida’s regulatory bodies involved in this process,” said Alford. “It helps to differentiate ourselves from other providers who have just met the bare minimum of power requirements.” Going forward, McKeen Towers said there will be a greater focus from the public on these types of systems and we will see the need to provide a marketable approach to encourage other corporate leadership to buy into investments beyond the standard. Alford said facilities must look at these systems not merely as a regulatory headache, but as a chance to prevent future issues during an emergency situation.
DEMAND RESPONSE 101
Demand Response (DR) or Demand Side Response (DSR) programs reduce demand on the utility supply in the event of a utility grid emergency. They do this by allowing the local electric utility — typically an Independent System Operator (ISO) or regional electric utility company — to automatically and remotely use an organization’s on-site generators, transferring some or all of a facility’s load from the grid to the generator. They also trigger load reduction through commercial and industrial building automation systems that act on lighting, HVAC and other mechanical loads.
While DR participants are only called upon to use their gen-sets up to four times per summer for about four hours per event, DR programs provide a no-risk, no-cost opportunity for organizations to help offset the capital and operational cost of a stationary generator set. Participants can earn money, save on energy costs and help maintain reliable electricity throughout their city, thereby avoiding blackouts or brownouts.
DR is most viable for natural gas generators rather than diesel generators, as the costs for achieving diesel emissions compliance in a nonemergency application often exceed the potential benefits of participating in a DR program. For example, in 2013 the U.S. Environmental Protection Agency (EPA) put forth rules to allow diesel generators to operate for 100 hours per year for DR purposes. A group of environmental regulators and advocates along with centralized generation interests appealed the rule to the U.S. Court of Appeals, which overturned the 100-hour limit in 2015. As a result, diesel generators must undergo costly upgrades to meet the emissions standards to run in DR applications.
DR program participants receive recurring capacity payments for agreeing to allow their local utility to curtail their utility power consumption in response to abnormally high electricity demand. They also receive additional energy payments based on their performance during dispatches.
Financial incentives vary, but DR can significantly offset the capex and opex of a generator system that would otherwise be viewed as just an insurance policy. For example, a 300 kW natural gas generator with approximately 200 kW of “enrolled load” would earn the customer $4000 at enrollment and up to $3000 per year for the peak energy generated.
Additionally, program participants usually pay less for electricity, whether they sign up for mandatory, voluntary or price-responsive programs. Rates may include a combination of credits, penalties or time-of-use charges, but they are generally lower overall for program participants. Two kinds of DR programs exist: those that are reliability-based and those that are economic-based.
Reliability-based programs pay you for load reduction when the electrical grid is stressed, such as during unplanned events like extreme heat, inclement weather and transmission outages. These programs are further categorized as either an Installed Capacity – Special Case Resource (ICAP-SCR) program or an Emergency Demand Response Program (EDRP).
The economic-based demand response programs give you the opportunity to offer load reduction into the electricity markets at any time, regardless of a reliability need. The economic-based DR programs are the Day-Ahead Demand Response Program (DADRP) and the Demand-Side Ancillary Services Program (DSASP).
In order to participate in the ICAP-SCR and EDRP programs, you must be able to reduce your load by at least 100 kW, unless you participate as part of a group of participants, in which case group must collectively meet the minimum 100 kW requirement. For these programs, the utility will send a notification a day before the event and on the day of the event, typically two hours prior to the load reduction period.
As an ICAP-SCR participant, performance is mandatory when notifications occur, and you will be obligated to reduce load for a minimum of four hours during the event. For EDRP programs, however, load reduction during any event is voluntary.
Participation in the DADRP and DSASP programs require you to reduce your load by at least 1 MW unless — as with the reliability-based programs — you participate as part of a group of participants, in which case the group must meet the minimum 1 MW requirement.
In the DADRP program, if you offer to reduce load and the offer is accepted and scheduled, then you are obligated to perform the load reduction as scheduled. In the DSASP program, participation is scheduled in the energy market and you are obligated to respond to real-time instructions to change load per directives. Real-time instructions for DSASP participants occur through continuous real-time communication.
In the Northeast, ISO New England, NYISO and Pennsylvania, New Jersey, Maryland Interconnect (PJM) typically manage the call for DR. However, utilities are increasingly outsourcing the monitoring and dispatch of assets to a third party, especially for commercial and industrial customers and generation.
Companies like CPOWER, EnerNOC, and IPKeys are commonly referred to as Energy Services Companies (ESCo). The ESCo will deploy an Energy Management System (EMS) to a client’s location for recording load, dispatching power generation assets and managing load. Working with an ESCo is often simpler for a commercial or industrial client, as the ESCo will understand the variable incentives offered by the ISO and the local utilities and help the client to maximize the economic benefit from their generator assets.
For more information about how you can participate in DR programs, contact your local utility, ISO or ESCo.
PRIME POWER, CONTINUOUS DUTY & CHP SOLUTIONS WITH SIEMENS
Did you know we offer Siemens gensets for prime power projects up to 2,000 kW in a single set with parallel capability to meet much larger requirements? Siemens Gensets are suitable for a broad range of commercial, industrial and municipal uses with long service intervals, easy maintenance and low fuel consumption. When it comes to Power Generation, Cogeneration/CHP, and Waste to Energy applications we have a solution that is robust and reliable and capable of working with any fuel you choose.
Watch Siemens video on CHP (Combined Heat Power)
Download brochures:
If you are interested in CHP, we have found the Siemens line to be an exceptional solution. All Siemens products offer great flexibility for load acceptance, are compliant with U.S. emissions standards and offer best in class efficiencies. To learn more contact us.